
HBS Group Southern completes M&E building services for 225 homes at the Plumer Estate on Salisbury Plain. Delivered by Lovell Partnerships in under 12 months, the Bulford SFA facilitated a smooth relocation of military personnel from Germany as part of the Army Basing Programme (ABP).
In 2018, Lovell Partnerships appointed HBS Group Southern’s M&E divisions to provide the mechanical and electrical services package for the Bulford Service Families’ Accommodation (SFA). Delivered under the Army Basing Programme (ABP), Bulford SFA was part of the UK’s largest and most complex military repatriation housing scheme which would provide a total of 917 homes for service personnel and their families.
It was vital for Lovell Partnerships to select an experienced mechanical and electrical contractor who could support the critical delivery of modern and sustainable accommodation being constructed for the Defence Infrastructure Organisation (DIO). Lovell recognised HBS Group Southern’s multi-disciplinary expertise within the new build housing sector and its proven ability to deliver professional, high-quality building services at a fast pace for the UK’s leading developers.
The UK industry standard for production is 1 to 4 houses per week. In 12 months, HBS’ Mechanical, Electrical and New Energies divisions worked collaboratively with Lovell Partnerships to complete and hand over 225 units at Bulford SFA in line with programme delivery targets. This equals the production output of 8 houses per week. That is 32 every 20 working days, unprecedented industry timescales.
Summary of new build M&E services
- HBS managed all aspects of supply, installation, testing and commissioning of the plumbing, heating and electrical system requirements for 225 properties.
- A dedicated project team made up of a site based contracts manager, site supervisor and new build plumbers and electricians worked in close collaboration with the Lovell site team to complete staged installs to a consistent quality standard in the safest manner possible, whilst meeting the client’s accelerated production levels.
- With a relentless focus on quality, we maintained high standards of workmanship during the fast-paced high-volume build through careful management, planning and strict quality control. Our on-site teams adhered to HBSGS in-house quality process during each stage of 1st fix, 2nd fix and final installation. This was backed up with a pre-occupation check before handing over to the client. We provided bespoke O&M handover packs and certification as standard.
- Built using a traditional, timber frame solution by Taylor Lane, all dwellings achieved an energy performance equal to Level 4 of the Code for Sustainable Homes.
- To meet local carbon reduction commitments, HBS New Energies in-house design team engaged early with the Lovell Partnerships project team to value engineer Bulford SFA’s solar requirements. We identified the most optimum plots across the MOD housing site and proposed a cost effective on-roof PV solution that met the client’s kWh total and 19% CO2 target.
-
Installed across 186 properties, the 607.2 kWp new build solar PV scheme at Bulford SFA will generate an estimated 535,000 kWh in annual zero carbon electricity and achieve a carbon saving of up to 268 tonnes per year. The large PV systems which maximise roof space will provide significant energy savings for the service families whilst support the DIO’s desire to combat fuel poverty.
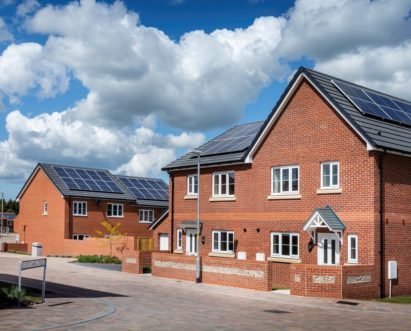
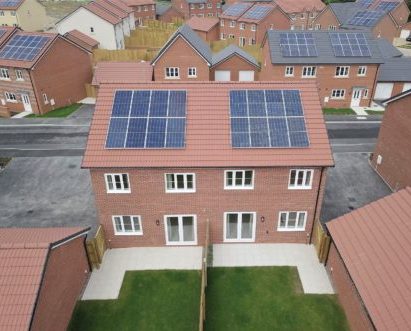
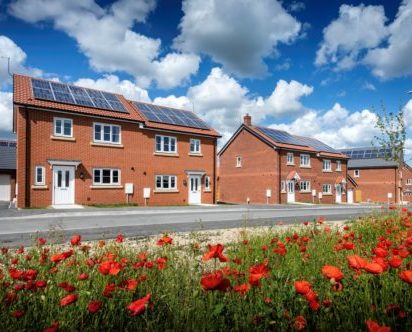
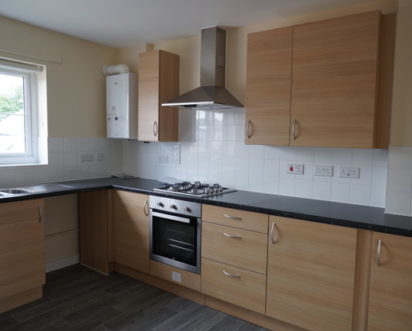
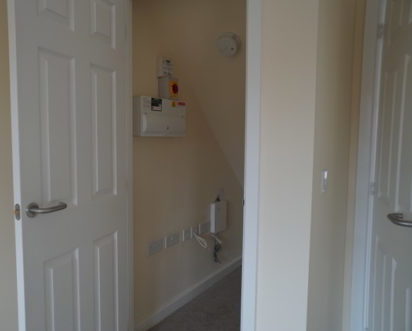
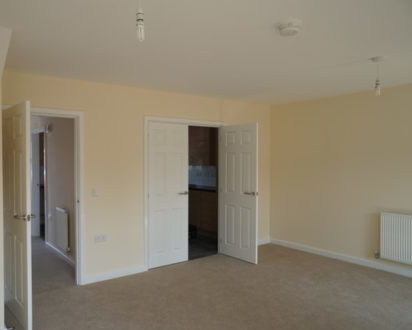
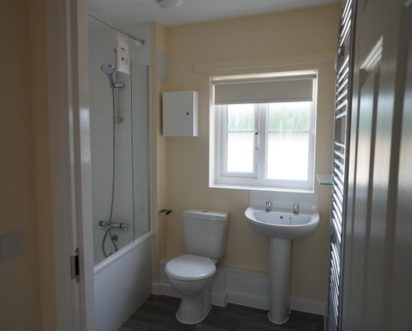
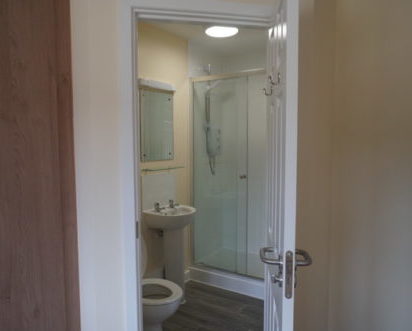
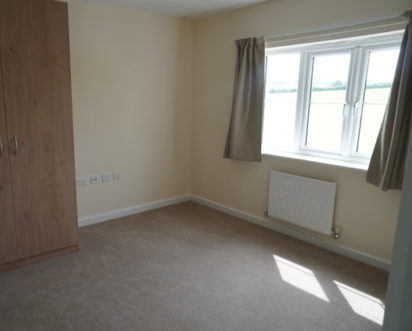